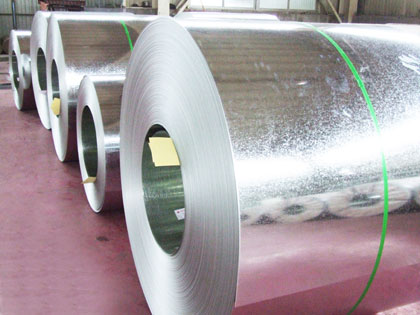
Two hot dip galvanizing lines, one is HR CGL with capacity of 400,000tpy, the other one is CR CGL with capacity of 300,000tpy: total capacity is 700,000tpy Strip specification of HR CGL is 23-4.0mm x 800-1350mm; while of CR CGL is 0. 2-2.3mm x 800-1350mm. The coating includes pure zinc coating and alloy coating and surface structure includes skin pass mill rolled spangle, little spangle, zero spangle surface treatment includes chrome passivation and/or oiling, chrome free passivation and/or oiling, chrome free anti-fingerprint
Standard, grade and purpose:
Type |
Steel grade |
Grade |
Product standard |
Grade in JIS G 3302 JFSA3011 |
Purpose |
Low carbon steel and
super low carbon steel
|
Commercial Quality (CQ) |
DX51D+Z |
GB/T 2518-2008 |
SGCC |
Used for common forming component |
Draw Quality(DQ) |
DX52D+Z |
SGCD1 |
Used for draw forming component |
||
Deep Draw qualty(DDQ) |
DX53D+Z |
SGCD2 |
Used for deep
draw forming component
|
||
Extra-Deep Draw
Qualty (EDOQ)
|
DX54D+Z |
SGCD3 |
Used for extra deep draw forming component | ||
Carbon structural steel
or low alloy steel
|
structural steel
(CQHSS)
|
S220GD+Z |
SGC340 |
Used for structural |
Product properties:
Grade |
Tensile test |
r90 min |
n90 min |
Coating adhesiveness |
||||
RcL |
Rm |
A80mm % min |
Bending diameter(a=strip thickness)
of different coating weight(g/㎡)
|
|||||
≦140/140 |
>140/140~ |
﹥175/175 |
||||||
DX51D+Z |
|
270~500 |
22 |
|
|
d=a |
d=a |
d=2a |
DX52D+Z |
140~300 |
270~420 |
26 |
|
|
|||
DX53D+Z |
140~260 |
270~380 |
30 |
|
|
|||
DX54D+Z |
120~220 |
270~350 |
36 |
1.6 |
0.18 |
Product properties:
Grade |
Tensile test |
Coating adhesiveness |
||
RcL |
Rm |
A80mm % |
180°Bending diameter(a=strip thickness) |
|
S220GD+Z |
220 |
300 |
20 |
d=a |
S250GD+Z |
250 |
330 |
19 |
d=a |
S280GD+Z |
280 |
360 |
18 |
d=2a |
S320GD+Z |
320 |
390 |
17 |
d=3a |
S350GD+Z |
350 |
420 |
16 |
d=3a |
S550GD+Z |
550 |
560 |
|
|
Product dimension,coil diameter,coil weight:
Type |
Nominal thickness |
Nominal width |
Coil O.D. |
Coil I.D. |
Weight T |
Common galvanizing(Z) |
0.25-4.0 |
800-1250 |
610 OR 508 |
900-2100 |
coil≤25 |
Zn-Al(ZA) |
0.25-1.5 |
800-1250 |
610 OR 508 |
900-2100 |
coil≤25 |
Nominal width(mm):
Yield strength min. |
Nominal thickness
mm
|
Thickness tolerance(mm) |
||||
Normal precision PT.A |
PT.B High precisionPT.B |
|||||
Nominal width(mm) | ||||||
≤1200 |
>1200-≤1500 |
>1500 |
≤1200 |
>1200-≤1500 |
||
﹤280 |
≤0.4 |
±0.05 |
±0.06 |
- |
±0.03 |
±0.04 |
>0.40-0.60 |
±0.06 |
±0.07 |
±0.08 |
±0.04 |
±0.05 |
|
>0.60-0.80 |
±0.07 |
±0.08 |
±0.09 |
±0.05 |
±0.06 |
|
>0.80-1.00 |
±0.08 |
±0.09 |
±0.10 |
±0.06 |
±0.07 |
|
>1.00-1.20 |
±0.09 |
±0.10 |
±0.11 |
±0.07 |
±0.08 |
|
>1.20-1.60 |
±0.10 |
±0.12 |
±0.12 |
±0.08 |
±0.09 |
|
>1.60-2.00 |
±0.13 |
±0.14 |
±0.14 |
±0.09 |
±0.10 |
|
>2.00-2.50 |
±0.15 |
±0.16 |
±0.16 |
±0.11 |
±0.12 |
|
>2.50-3.00 |
±0.17 |
±0.18 |
±0.18 |
±0.12 |
±0.13 |
|
>3.00-4.00 |
±0.20 |
±0.20 |
±0.20 |
±0.15 |
±0.15 |
|
≥280 |
≤0.4 |
±0.06 |
±0.07 |
- |
±0.04 |
±0.05 |
>0.40-0.60 |
±0.07 |
±0.08 |
±0.09 |
±0.05 |
±0.06 |
|
>0.60-0.80 |
±0.08 |
±0.09 |
±0.11 |
±0.06 |
±0.06 |
|
>0.80-1.00 |
±0.09 |
±0.11 |
±0.12 |
±0.07 |
±0.07 |
|
>1.00-1.20 |
±0.11 |
±0.12 |
±0.13 |
±0.08 |
±0.09 |
|
>1.20-1.60 |
±0.13 |
±0.14 |
±0.14 |
±0.09 |
±0.11 |
|
>1.60-2.00 |
±0.15 |
±0.17 |
±0.17 |
±0.11 |
±0.12 |
|
>2.00-2.50 |
±0.18 |
±0.19 |
±0.19 |
±0.13 |
±0.14 |
|
>2.50-3.00 |
±0.20 |
±0.21 |
±0.21 |
±0.14 |
±0.15 |
|
>3.00-4.00 |
±0.22 |
±0.24 |
±0.25 |
±0.20 |
±0.21 |
Note:For cold-rolled wide strip in the weld zone within 15m of thickness tolerances than the specified value on the table is 60% larger.
Width tolerance:
Nominal width mm |
Width tolerance(mm) |
|||
Normal precision PW.A |
High precision PW.B |
|||
Min |
Max |
Min |
Max |
|
≥600-1200 |
0 |
+5 |
0 |
+2 |
>1200-1500 |
0 |
+6 |
0 |
+2 |
Length tolerance:
Nominal length |
Length tolerance(mm) |
|||
Normal precision PL.A |
High precision PL.B |
|||
Min |
Max |
Min |
Max |
|
﹤2000 |
0 |
+6 |
0 |
+3 |
≥2000 |
0 |
lenght of 0.3% |
0 |
lenght of 0.15% |
Flatness
flatness of galvanized strip with minimum yield strength <280Mpa:
Nominal width |
Flatness,not greater than(mm) |
|||||
Normal precision PF.A |
High precision PF.B |
|||||
Nominal thickness |
||||||
﹤0.7 |
≥0.7~1.2 |
≥1.2 |
﹤0.7 |
≥0.7~1.2 |
≥1.2 |
|
≥600~1200 |
12 |
10 |
8 |
5 |
4 |
3 |
≥1200~1500 |
15 |
12 |
10 |
6 |
5 |
4 |
≥1500 |
19 |
17 |
15 |
8 |
7 |
6 |
Flatness of galvanized strip with minimum yield strength =280~360Mpa:
Nominal width |
Flatness,not greater than(mm) |
|||||
Normal precision PF.A |
High precision PF.B |
|||||
Nominal thickness |
||||||
﹤0.7 |
≥0.7~1.2 |
≥1.2 |
﹤0.7 |
≥0.7~1.2 |
≥1.2 |
|
≥600~1200 |
15 |
13 |
10 |
8 |
6 |
5 |
≥1200~1500 |
18 |
15 |
13 |
9 |
8 |
6 |
≥1500 |
22 |
20 |
19 |
12 |
10 |
9 |
Coating weight:
Surface structure |
Coating grade |
Double sides coaing weight.min.g/㎡ |
Coating weight theoretical reference value,single point per side |
Density g/㎝2 |
||
Three-points test |
Single-point test |
Typical value |
Range |
7.1 |
||
Pure zinc coating |
Z100 |
100 |
85 |
7 |
5~12 |
|
Z140 |
140 |
120 |
10 |
7~15 |
||
Z200 |
200 |
170 |
14 |
10~20 |
||
Z225 |
225 |
195 |
16 |
11~22 |
||
Z275 |
275 |
235 |
20 |
15~27 |
||
Z450 |
450 |
385 |
32 |
24~42 |
||
Z600 |
600 |
510 |
42 |
32~55 |
Coatinglayer surface structure:
Surface structure |
Code |
Instuctons |
Pupose |
Normal spangle |
N |
In common condition,zinc layer cools down and condensates into spangles after galvanizing. |
Common purpose |
Zero spangle |
M |
Adopts a special process to interfere solidification of coating metal to get required surface structure.In this way only tiny spangles sometimes invisible formed. |
Used in case that normal spangle cannot meet appearance requirements. |
Skin pass mill rolled |
SP |
Coating structure after rolled by skin pass mill,it has no metallic luster which is benefit for improving appearance or decoration painting. |
Used in case to satisfy high requirement of surface quality, also can be used for base metal of color coating. |
Surface treatment and feature:
Surface treatment type |
Code |
Instuctons |
Chemical passivation |
C |
Chemical passivation is to protect product surface not contact with moisture air,so as to reduce risk of rust during storage and transportation. |
EC |
||
Oiling |
O |
Oiling can reduce risk of corrosion so as to improve anti-corrosion ability of product. |
Chemical passivation +oiling |
CO |
Oiling after passivation can further improve anti-corrosion ability of product. |
ECO |
||
Anti-fingerprint(roll coater) |
S |
Through coating one thin layer of organic film with each side 1~2g/m2,it can improve property of anti-corrosion,anti-fingerprint,solvent resistance and high conductivity,etc.In addition,when forming,it can improve lubrication property.It can also be base of further coating. |
ES |
||
Phosphorization(roll coater) |
P |
It can be preparation of further painting and has function of lubrication;it can also reduce risk of rust during storage and transportation. |
Phosphorization+oiling |
PO |
Further reduce risk of rust and can improve lubrication property. |
Without surface treatment |
u |
Without any anti-rust treatment.Only in case that customer will undertake risk of rust by themselves. |
Note:EC,ECO,ES belongs to environment protection products.
Surface quality refers to company standard and rules as below:
Surface grade |
Feature |
FA |
Following defects are acceptable such as tiny zinc grain,scratch,imprint,uneven color,black point,air wiper wale,passivation light spot,wale occurred due to tension leveling,zinc flow,etc. |
FB |
Defects in small range is acceptable such as imprint by skin pass mill,slight scratch,tiny spangle,zinc flow wale,passivation mark, etc. |
FC |
The side under control should not influence the uniform appearance of painting;the other side should reach level B at least. |
Note:A: without treatment of SPM,B,C:with treatment of SPM
Tensile strain mark: